Геометрия, доступная для лазерной стереолитографии
Возможности SLA-технологии по изготовлению прототипов сложной геометрии
Глядя на принцип работы стерелитографической машины, может сложиться впечателение, что изготовить таким способом можно прототип совершенно любой геометрической формы. В самом деле, прототип выращивается послойно, а каждый слой формируется лазерным пучком на поверхности смолы. Поэтому разбить на слои и затем послойно нарисовать можно теоретически любую трёхмерную фигуру.
В большинстве случаев теория сходится с практикой. Именно поэтому SLA-технология является RP-технологией, поскольку процесс получения прототипа в наименьшей степени зависит от его формы, в отличие от традиционных технологий. Однако "и на солнце бывают пятна".
Существует ряд ограничений по геометрии, предполагаемой к выращиванию по SLA-технологии. Знать эти ограничения полезно заказчику, чтобы не требовать невозможного, яснее представлять процесс получения его детали и корректировать требуемую модель - разбить её на части или изменить формы непринципиальных элементов.
Диаметр лазерного пучка - 0.3мм
Итак, во-первых, нужно сказать о рабочем инструменте - лазере. Диаметр пучка - 0.3мм. Соотвественно, элементы меньше 0.3мм просто невозможно нарисовать на поверхности смолы. Поэтому например, текст с буквами, имеющими штрихи толщиной меньше 0.3мм можно выполнить только "утопленным" в поверхность. Лазерный пучок штрихуя поверхность, будет обходить буквы с точностью до 50 мкм и отрисует их. Выступающим же текст сделать не получится - поскольку все штрихи толщиной 0.3 мм сделать невозможно, они будут проигнорированы программой.
При выполнении измерений используются методика МИ 1317-2004.
Усадка - причина коробления тонких деталей
Затем нужно вспомнить про усадку. Поскольку в процессе отверждения материал переходит из жидкого состояния в твёрдое, его плотность повыышается. В результате линия, рисуемая лазерным лучом на поверхности смолы при его движении стремится стянуться на микрорасстояние. Поскольку при любом штриховании лазер рисует множество линий, приполимеризованных к нижним слоям, каждый новый слой стремится стянуть предыдущий. В результате в материале возникают внутренние напряжения. Обычно они компенсируются прочностными свойствами самого материала. То есть боковые стенки и элементы, работающие как ребра жесткости, вопринимают на себя напряжение от усадки и не дают детали коробится. Поэтому лучшей геометрией для стереолитографии являются детали типа массив, то есть имеющие равные размеры по всем трём измерениям. Например такие:
 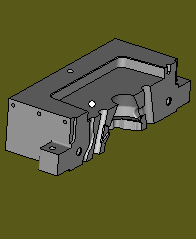
Если же деталь соотвествует типу поверхность, то есть одно измерение крайне мало, то напряжения, вызванные усадкой, не смогут быть скомпенсированы и деталь с высокой вероятностью покоробится. Уменьшить риск коробления можно, если выращивать модель "стоя", тогда усадочные напряжения будут минимальными и распределены в направлении длинной стороны, которую сложно изогнуть. Однако это значительно увеличит время выращивания. Кроме того, на стадии проектирования можно добавить рёбра жесткости, чтобы увеличить жесткость.
Подпорки нужны к любым деталям
Это наверное всё, что касается формы геометрии. В заключение нужно рассказать о таком необходимом элементе, как подпорки. Это технологические элементы, которые удерживают только что сформированную лазером на поверхности жидкости тонкую твёрдую пленку от уплывания. Поскольку толщина слоя 0.1мм, то эта пленка может легко быть сдвинута ножом или даже гидродинамическими течениями при движении платформы. Поэтому любая большая поверхность, близкая к горизонтальной, выращивается на подпорках. Подпорки формируются также как и деталь лазером в виде тонких стеночек с зубчиками. Зубчики нужны для того, чтобы подпорку можно было легко отломать, не повредив при этому деталь. Это, кстати, накладывает ещё одно ограничение на прототип: нежелательны элементы толщиной менее 1мм, поскольку при отламывании подпорок (толщиной 0.3мм) они с большой вероятностью будут повреждены. Желательно, чтобы подпираемая поверхность была простая по конфигурации, прочная и неответственная, ведь после отламывания останутся корешки зубчиков, которые удаляются шлифованием. Со сложной ответственной поверхностью могут возникнуть трудности. Поэтому такие поверхности желательно располагать "лицом вверх", чтобы подпорок на них не было изначально.
Ну и последнее, о чём надо помнить - подпорки нужно как-то удалить из детали после выращивания. В качестве примера можно привести полый куб. Для выращивания нужно будет непременно поддержать подпорками верхнюю стенку изнутри. После выращивания остатки смолы будут слиты через отверстия, но извлеч подпорки не удастся никак. Подобные детали можно изготавливать только по частям с последующей склейкой. Конечно это пример скорее "из области фантастики", но о том, как будут извлекаться подпорки нужно всегда помнить при проектировании прототипа.
|